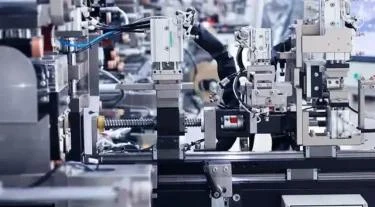
# Tape Production Process and Techniques
## Introduction to Tape Manufacturing
Tape manufacturing is a complex process that involves multiple stages to produce high-quality adhesive products. From industrial applications to everyday household use, tapes serve various purposes, making their production techniques crucial for meeting diverse market demands.
## Raw Material Selection
The foundation of quality tape production lies in careful raw material selection:
– Backing materials (paper, plastic films, cloth, or foil)
– Adhesive compounds (rubber-based, acrylic, or silicone)
– Release liners and coatings
– Additives for specific properties
## The Tape Production Process
### 1. Backing Material Preparation
The process begins with preparing the backing material. Plastic films may be extruded or cast, while paper and cloth backings undergo specific treatments to enhance strength and adhesion properties.
### 2. Coating Application
The prepared backing material then receives the adhesive coating through one of several methods:
– Direct coating: Adhesive is applied directly to the backing
– Transfer coating: Adhesive is first applied to a release liner then transferred
– Hot melt coating: Adhesive is applied in molten form
### 3. Drying and Curing
After coating, the tape passes through drying ovens or curing chambers to remove solvents and achieve proper adhesive properties. Temperature and duration vary based on adhesive type.
### 4. Slitting and Rewinding
The large rolls of coated material are then slit into narrower widths using precision cutting equipment. This stage requires careful tension control to ensure clean edges and consistent product quality.
### 5. Packaging
Finished tape rolls are packaged according to customer specifications, which may include individual boxes, bulk packaging, or custom dispensers.
## Advanced Manufacturing Techniques
Modern tape production incorporates several advanced techniques:
### Multi-layer Coating
Some tapes require multiple adhesive layers or special coatings to achieve desired properties like UV resistance or enhanced bonding.
### Pattern Coating
Instead of full-surface application, adhesives can be applied in specific patterns to control adhesion strength or allow breathability.
### Automated Quality Control
Vision systems and sensors continuously monitor product quality throughout production, detecting defects in real-time.
## Environmental Considerations
Sustainable tape manufacturing has become increasingly important:
– Water-based adhesives replacing solvent-based formulations
– Recyclable backing materials
– Energy-efficient drying systems
– Waste reduction through precision application
## Future Trends in Tape Production
The industry continues to evolve with:
– Development of smarter adhesives with responsive properties
– Nanotechnology applications for enhanced performance
– Increased automation and Industry 4.0 integration
– Biodegradable and compostable tape options
Understanding these production processes and techniques helps manufacturers create tapes that meet ever-changing market needs while maintaining high quality and performance standards.
Keyword: tape manufacturing