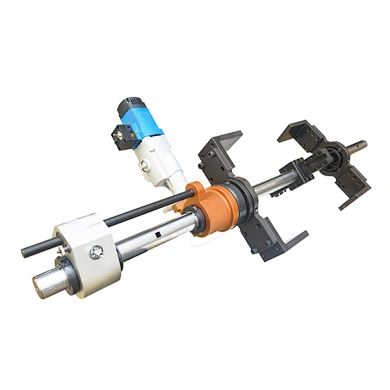
,文章长度在1000字左右
# Flange Facer Machine: Essential Equipment for Pipe Flange Resurfacing
## Introduction to Flange Facer Machines
Flange facer machines are specialized tools designed for resurfacing pipe flanges to ensure proper sealing and alignment in piping systems. These powerful machines play a critical role in maintenance and repair operations across various industries, including oil and gas, petrochemical, power generation, and shipbuilding.
The primary function of a flange facer is to machine the sealing surface of a flange to restore its flatness and surface finish after damage or wear. This process is essential for preventing leaks and maintaining system integrity in high-pressure applications.
## How Flange Facer Machines Work
Flange facers operate by mounting directly onto the pipe flange and using cutting tools to remove material from the sealing surface. The machine typically consists of:
– A rigid frame that clamps to the flange
– A rotating cutting head with adjustable tool bits
– A drive mechanism (manual, electric, or hydraulic)
– Precision adjustment systems for depth control
The cutting process creates a perfectly flat surface with the required surface finish, typically between 125 and 250 microinches Ra for most gasket applications. Modern machines can achieve tolerances within 0.001 inches per foot of diameter.
## Types of Flange Facer Machines
### 1. Portable Flange Facers
These lightweight, compact machines are designed for field use and can be easily transported to job sites. They’re ideal for maintenance work in confined spaces or remote locations.
### 2. Stationary Flange Facers
Larger, more powerful machines designed for shop use. These typically offer higher precision and can handle larger diameter flanges than portable units.
### 3. CNC Flange Facers
Computer-controlled machines that provide the highest level of precision and repeatability. These are commonly used in manufacturing environments where large quantities of flanges need processing.
## Key Features to Consider When Selecting a Flange Facer
When choosing a flange facing machine, several factors should be considered:
Keyword: flange facer machines
– Flange diameter range
– Power source (manual, electric, pneumatic, or hydraulic)
– Cutting speed and feed rate
– Weight and portability
– Tooling options and availability
– Ease of setup and operation
– Safety features
## Applications of Flange Facing Machines
Flange facers are used in numerous industrial applications:
– Pipeline maintenance and repair
– Power plant maintenance
– Refinery turnaround operations
– Shipbuilding and repair
– Chemical processing plants
– Water treatment facilities
The ability to perform on-site flange resurfacing saves significant time and money compared to removing and replacing damaged flanges.
## Benefits of Using Flange Facer Machines
Investing in quality flange facing equipment offers several advantages:
– Cost savings by repairing rather than replacing flanges
– Reduced downtime for critical systems
– Improved safety by ensuring proper sealing
– Versatility to handle various flange sizes and materials
– Portability for field service applications
– Consistent, high-quality results
## Maintenance and Care of Flange Facers
Proper maintenance ensures long service life and consistent performance:
– Regular cleaning to remove metal chips and debris
– Lubrication of moving parts as specified by the manufacturer
– Inspection and replacement of worn cutting tools
– Proper storage in dry, clean conditions
– Periodic calibration checks for precision machines
## Safety Considerations
When operating flange facers, always follow these safety guidelines:
– Wear appropriate PPE (safety glasses, gloves, hearing protection)
– Secure the workpiece properly before starting
– Ensure all guards are in place
– Follow lockout/tagout procedures when servicing
– Never exceed the machine’s rated capacity
– Be aware of rotating parts and pinch points
## Future Trends in Flange Facing Technology
The flange facing industry continues to evolve with new technologies:
– Advanced materials for longer-lasting cutting tools
– Improved portability