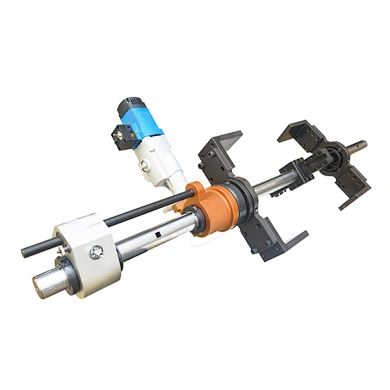
,字数1000字左右
# On-Site Flange Machining Services
## What is On-Site Flange Machining?
On-site flange machining refers to the process of repairing, resurfacing, or modifying flanges at their installed location rather than removing them and sending them to a machine shop. This specialized service is performed by trained technicians using portable machining equipment designed specifically for field work.
Flanges are critical components in piping systems, serving as connection points between pipes, valves, pumps, and other equipment. Over time, flanges can become damaged, warped, or corroded, leading to leaks and potential system failures. On-site machining provides an efficient solution to these problems without the need for costly system shutdowns and component removal.
## Benefits of On-Site Flange Machining
Choosing on-site flange machining services offers numerous advantages over traditional repair methods:
– Reduced Downtime: Systems can remain operational or experience significantly shorter shutdown periods
– Cost Savings: Eliminates transportation costs and reduces labor expenses
– Precision Work: Modern portable equipment delivers machine-shop quality results
– Safety: Minimizes risks associated with disassembly and transportation
– Flexibility: Services can be performed in remote or hard-to-access locations
– Environmental Benefits: Reduces the carbon footprint associated with transportation
Keyword: On-site flange machining
## Common On-Site Flange Machining Services
Professional on-site machining companies typically offer a range of flange-related services:
### 1. Flange Facing
This process resurfaces the sealing area of a flange to restore its flatness and ensure proper sealing. Portable flange facers can handle diameters from small bore pipes up to several meters in size.
### 2. Bolt Hole Repair
Damaged or elongated bolt holes can be repaired by machining them to a larger size and installing bushings or inserts to restore proper fit and function.
### 3. Flange Reconditioning
This comprehensive service may include facing, bolt hole repair, and other restoration work to bring a flange back to like-new condition.
### 4. Custom Machining
For unique situations, technicians can perform custom machining operations to modify flanges for specific applications or to accommodate unusual damage patterns.
## Industries That Benefit from On-Site Flange Machining
Numerous industries rely on on-site flange machining services to maintain their operations:
– Oil and Gas: Both upstream and downstream operations
– Power Generation: Nuclear, fossil fuel, and renewable energy plants
– Chemical Processing: Production facilities and storage terminals
– Marine: Shipboard systems and offshore platforms
– Water Treatment: Municipal and industrial water systems
– Manufacturing: Process piping in various industrial settings
## The On-Site Machining Process
A typical on-site flange machining project follows these general steps:
– Initial Assessment: Technicians evaluate the flange condition and determine the required work
– Equipment Setup: Portable machines are positioned and secured to the work area
– Machining: The actual cutting or resurfacing operation is performed
– Quality Control: Measurements are taken to ensure specifications are met
– Cleanup: The work area is cleaned and prepared for return to service
– Documentation: A detailed report of the work performed is provided
## Choosing an On-Site Flange Machining Provider
When selecting a service provider, consider these important factors:
– Experience: Look for companies with extensive field experience
– Equipment Quality: Ensure they use modern, well-maintained machines
– Certifications: Check for relevant industry certifications and safety records
– Response Time: Evaluate their ability to respond quickly to emergencies
– Technical Expertise: Assess their knowledge of various flange types and materials
– Safety Record: Verify their commitment to safe work practices
## Future Trends in On-Site Flange Machining
The field of on-site flange machining continues to evolve with technological advancements:
– Improved portability of equipment for easier access to confined spaces
– Enhanced precision through digital controls and measurement systems
– Integration with 3D scanning for more accurate assessments