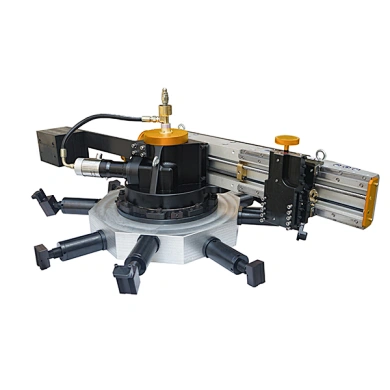
# Industrial Flange Facer: Essential Tool for Precision Machining
## Introduction to Industrial Flange Facers
Industrial flange facers are specialized machines designed to create perfectly flat and smooth surfaces on pipe flanges. These powerful tools play a critical role in ensuring proper sealing and alignment in piping systems across various industries. From oil and gas to chemical processing plants, flange facers help maintain the integrity of critical connections that must withstand high pressures and temperatures.
## How Flange Facers Work
The operation of an industrial flange facer involves several precise steps:
1. The machine is securely mounted onto the flange surface
2. Cutting tools are positioned and adjusted for the required facing operation
3. The rotating cutting head removes material to create a uniform surface
4. Finishing passes ensure the required surface finish is achieved
Modern flange facers often incorporate advanced features like digital readouts, automatic feed controls, and tool positioning systems to enhance accuracy and efficiency.
## Key Applications in Industry
Industrial flange facers serve numerous essential functions:
– Preparing new flanges for installation
– Resurfacing damaged or corroded flange faces
– Creating special groove patterns for specific gasket types
– Maintaining critical sealing surfaces in high-pressure systems
These machines are particularly valuable in industries where flange connections must meet strict quality standards, such as nuclear power plants or offshore drilling platforms.
## Advantages of Using Professional Flange Facing Equipment
Investing in quality industrial flange facers offers several significant benefits:
– Improved sealing performance and reduced leakage risks
– Extended service life of flange connections
– Cost savings by refurbishing rather than replacing flanges
– Compliance with industry standards and regulations
– Increased safety in high-pressure applications
Professional-grade machines also offer greater precision and repeatability compared to manual methods, ensuring consistent results across multiple flanges.
## Choosing the Right Flange Facer
Keyword: Industrial flange facer
When selecting an industrial flange facer, consider these important factors:
– Flange size range the machine can accommodate
– Power requirements and available power sources
– Portability needs for field work
– Material capabilities (carbon steel, stainless steel, etc.)
– Required surface finish quality
– Available accessories and tooling options
Higher-end models may offer features like CNC controls, automatic tool changers, and integrated measurement systems for the most demanding applications.
## Maintenance and Safety Considerations
Proper maintenance ensures optimal performance and longevity of flange facing equipment:
– Regular lubrication of moving parts
– Timely replacement of worn cutting tools
– Cleaning of chips and debris after each use
– Periodic calibration checks
– Proper storage when not in use
Safety precautions should always include:
– Wearing appropriate PPE (safety glasses, gloves, etc.)
– Securing the workpiece properly
– Following manufacturer’s operating instructions
– Maintaining a clean work area
– Using machine guards as provided
## The Future of Flange Facing Technology
As industries demand higher precision and efficiency, flange facing technology continues to evolve. Emerging trends include:
– Increased automation and robotic integration
– Advanced materials for longer-lasting cutting tools
– Smart sensors for real-time process monitoring
– Portable units with greater power and capability
– Environmentally friendly designs with reduced energy consumption
These advancements will further enhance the role of industrial flange facers in maintaining critical piping infrastructure across multiple sectors.