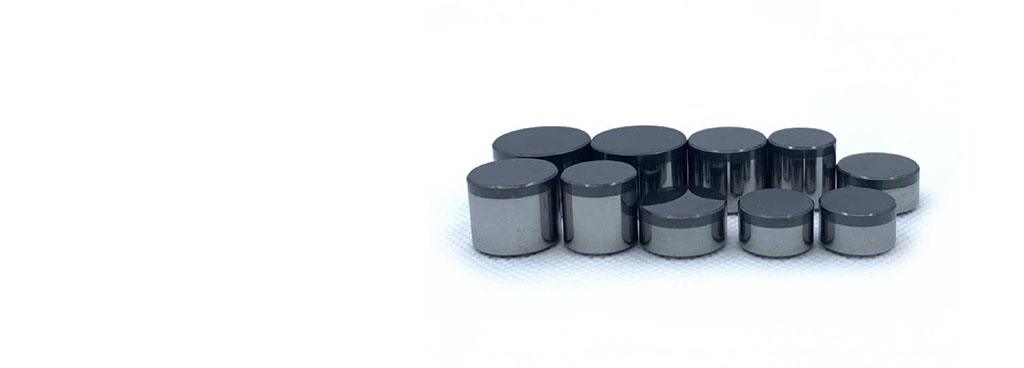
# Optimizing Performance of PDC Cutters in Drilling Operations
## Introduction
Polycrystalline Diamond Compact (PDC) cutters have revolutionized the drilling industry with their exceptional hardness, wear resistance, and thermal stability. These cutting elements are crucial components in modern drill bits, enabling faster and more efficient drilling operations across various formations.
## Understanding PDC Cutter Technology
Composition and Structure
PDC cutters consist of a synthetic diamond layer bonded to a tungsten carbide substrate. The diamond layer is composed of micron-sized diamond crystals sintered together under high pressure and temperature, creating an extremely hard and durable cutting surface.
Key Performance Characteristics
The effectiveness of PDC cutters depends on several factors:
- Diamond table thickness
- Thermal stability
- Impact resistance
- Wear resistance
- Interface bond strength
Keyword: cutter pdc
## Factors Affecting PDC Cutter Performance
Formation Characteristics
The geological formation being drilled significantly impacts cutter performance. Hard, abrasive formations require different cutter specifications compared to softer formations.
Drilling Parameters
Optimal weight on bit (WOB), rotational speed (RPM), and hydraulic conditions must be carefully balanced to maximize cutter life and drilling efficiency.
Thermal Management
Excessive heat generation can lead to premature cutter failure. Proper cooling and fluid circulation are essential for maintaining cutter integrity.
## Optimization Strategies
Cutter Geometry and Orientation
Strategic placement and orientation of cutters on the bit face can significantly improve cutting efficiency and reduce wear patterns.
Advanced Materials
Recent developments in PDC technology include:
- Thermally stable diamond formulations
- Enhanced interface designs
- Novel substrate materials
Bit Design Integration
PDC cutter performance is maximized when integrated with optimized bit designs that consider:
- Hydraulic flow characteristics
- Cutter exposure and redundancy
- Stability features
## Field Performance Monitoring
Wear Pattern Analysis
Regular inspection of used cutters provides valuable insights for performance optimization. Common wear patterns include:
- Uniform wear
- Chipping
- Delamination
- Thermal degradation
Real-time Data Utilization
Modern drilling operations incorporate real-time monitoring systems to track cutter performance and adjust drilling parameters accordingly.
## Future Developments
The PDC cutter technology continues to evolve with research focusing on:
- Nanostructured diamond materials
- Self-sharpening cutter designs
- Intelligent cutters with embedded sensors
- Improved thermal management systems
## Conclusion
Optimizing PDC cutter performance requires a comprehensive approach that considers material science, bit design, drilling parameters, and formation characteristics. As technology advances, PDC cutters will continue to push the boundaries of drilling efficiency and reliability in increasingly challenging environments.