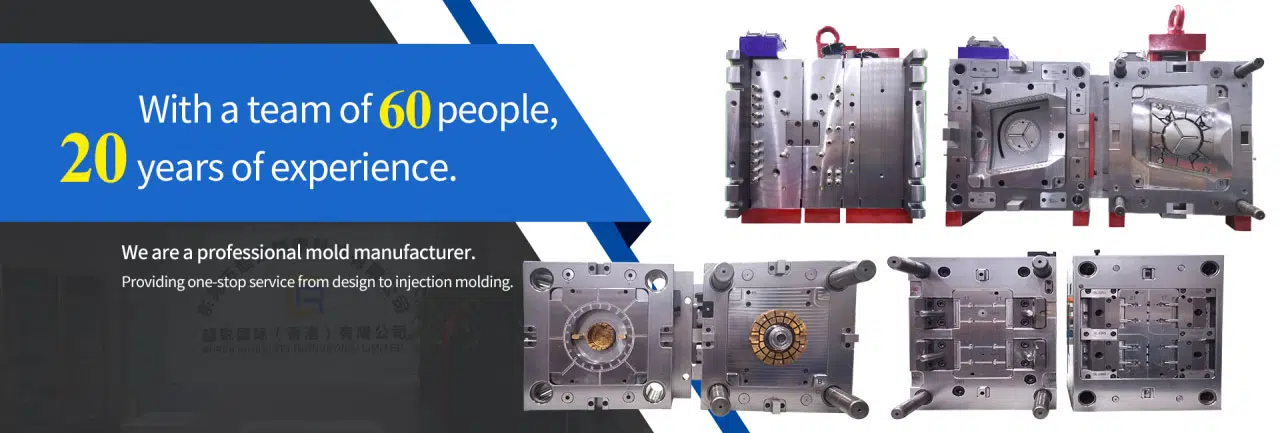
# Design for Manufacturing Analysis in Product Development
## The Importance of DFM Analysis
Design for Manufacturing (DFM) analysis has become a critical component in modern product development processes. By integrating manufacturing considerations early in the design phase, companies can significantly reduce production costs, improve product quality, and accelerate time-to-market.
DFM analysis examines how design choices affect manufacturing processes, identifying potential issues before they become costly problems during production. This proactive approach helps bridge the gap between design intent and manufacturing reality.
## Key Principles of DFM Analysis
Effective DFM analysis follows several fundamental principles:
– Simplify designs to reduce part count and assembly complexity
– Standardize components and materials whenever possible
– Optimize tolerances to balance performance and manufacturability
– Design for the most appropriate manufacturing process
– Consider assembly sequence and accessibility
## Benefits of Implementing DFM
Companies that consistently apply DFM analysis in their product development cycle experience numerous advantages:
### Cost Reduction
DFM helps minimize material waste, reduce labor requirements, and decrease tooling costs. By designing products that are easier to manufacture, companies can achieve significant savings throughout the product lifecycle.
### Quality Improvement
Products designed with manufacturing in mind typically have fewer defects and higher reliability. DFM analysis helps identify potential quality issues before production begins, leading to better overall product performance.
### Faster Time-to-Market
By addressing manufacturing challenges early, DFM reduces the need for costly redesigns and production delays. This streamlined approach allows companies to bring products to market more quickly while maintaining high quality standards.
## Common DFM Analysis Techniques
Several methodologies support effective DFM implementation:
– Process capability analysis
– Design for Assembly (DFA) evaluation
– Tolerance stack-up analysis
– Material selection optimization
– Tooling and fixture considerations
## Challenges in DFM Implementation
While DFM offers significant benefits, companies often face obstacles in its adoption:
– Resistance to change from design teams accustomed to traditional methods
– Lack of manufacturing expertise among designers
– Difficulty quantifying DFM benefits in financial terms
– Time constraints in early design phases
– Communication gaps between design and manufacturing teams
## Best Practices for Successful DFM
To maximize the effectiveness of DFM analysis, organizations should:
– Involve manufacturing engineers early in the design process
– Establish clear DFM guidelines and checklists
– Use cross-functional teams to evaluate designs
– Leverage DFM software tools for automated analysis
– Continuously update DFM knowledge based on production feedback
Keyword: DFM Analysis
## The Future of DFM Analysis
As manufacturing technologies evolve, DFM analysis continues to advance. Emerging trends include:
– Integration with digital twin technologies
– AI-powered DFM recommendations
– Cloud-based collaborative DFM platforms
– Automated manufacturability scoring systems
– Real-time DFM feedback during CAD modeling
By embracing these innovations, companies can further enhance their product development processes and maintain competitive advantages in increasingly demanding markets.