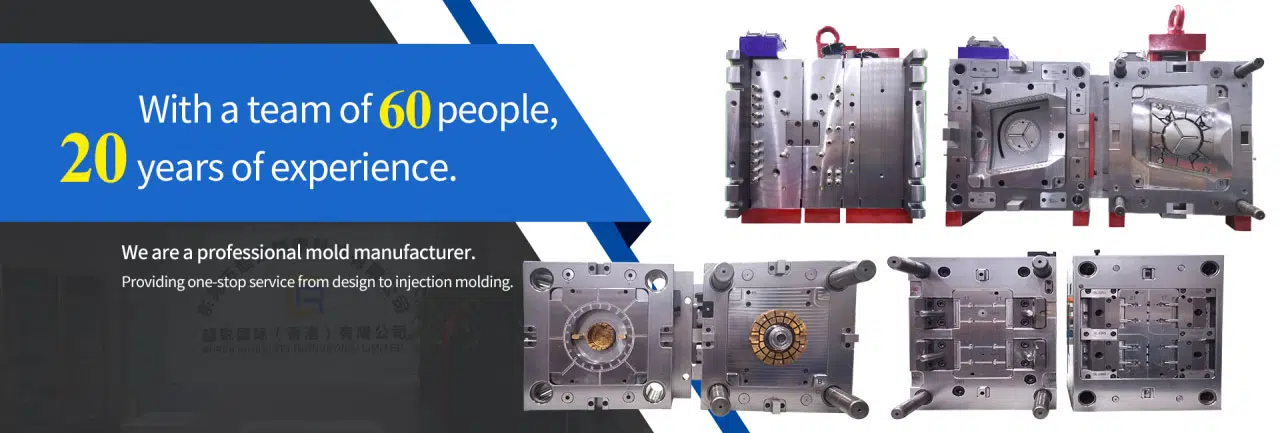
# Precision Engineering: Mastering Tight Tolerances for Optimal Performance
## The Importance of Tight Tolerances in Modern Manufacturing
In today’s highly competitive manufacturing landscape, tight tolerances have become a critical factor in determining product quality and performance. These precise measurements refer to the permissible limit of variation in a physical dimension, ensuring components fit together perfectly and function as intended.
## Understanding Tolerance Standards
Tolerance standards vary across industries, with some requiring exceptionally tight specifications:
– Aerospace components often demand tolerances within ±0.0001 inches
Keyword: Tight Tolerances
– Medical devices typically require ±0.0005 inches
– Automotive parts usually fall between ±0.001 to ±0.005 inches
– Consumer goods may allow ±0.010 inches or more
## Challenges in Achieving Tight Tolerances
Manufacturers face several obstacles when working with extremely tight tolerances:
Thermal expansion becomes a significant factor as materials expand and contract with temperature changes. Even small variations can push components out of spec. Machine tool accuracy must be exceptional, often requiring regular calibration and maintenance. Material selection also plays a crucial role, as some materials are more stable and predictable than others.
## Advanced Techniques for Maintaining Precision
Modern manufacturers employ various strategies to achieve and maintain tight tolerances:
1. Computer Numerical Control (CNC) Machining
CNC machines offer repeatable accuracy down to micrometer levels when properly maintained and programmed. Advanced CNC systems can compensate for tool wear and thermal effects in real-time.
2. Coordinate Measuring Machines (CMM)
These sophisticated measurement devices verify dimensional accuracy with extreme precision, often using laser or touch probe technology to validate parts against CAD models.
3. Statistical Process Control (SPC)
SPC methods monitor production processes to detect variations before they exceed tolerance limits, allowing for timely adjustments.
## The Future of Tight Tolerance Manufacturing
Emerging technologies promise even greater precision capabilities:
Additive manufacturing (3D printing) is achieving increasingly tight tolerances, with some metal printing systems now capable of ±0.002 inches. Nanotechnology is pushing boundaries further, enabling manipulation at the molecular level. Smart factories with IoT-connected equipment will provide real-time monitoring and automatic adjustments to maintain tight tolerances throughout production runs.
## Conclusion
Mastering tight tolerances requires a combination of advanced equipment, skilled operators, rigorous quality control, and continuous process improvement. As products become more complex and performance demands increase, the ability to maintain precise tolerances will remain a key differentiator for manufacturers across all industries.