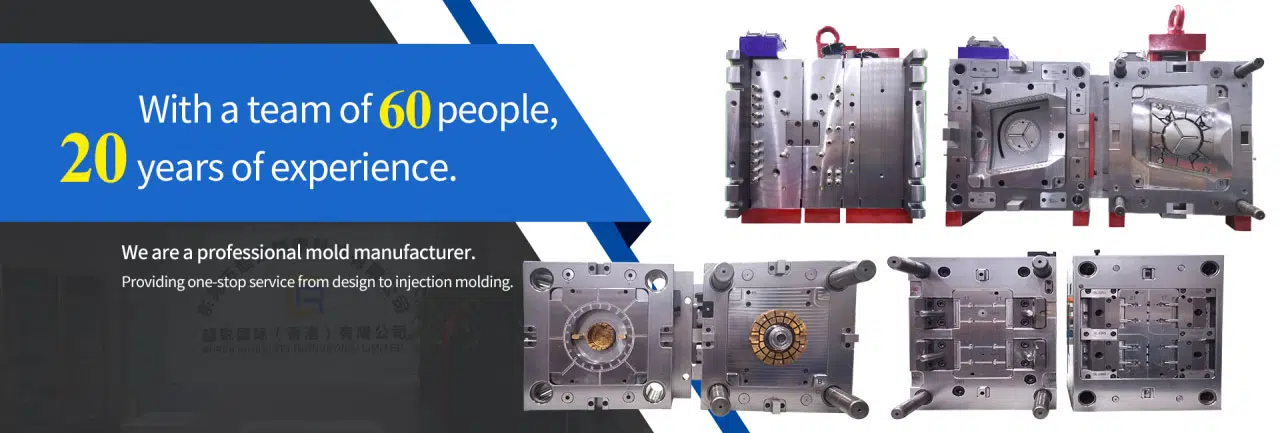
# Injection Molding: Process, Materials, and Applications
## Introduction to Injection Molding
Injection molding is a widely used manufacturing process for producing plastic parts in large volumes. This process involves injecting molten material into a mold where it cools and solidifies into the desired shape. Due to its efficiency and versatility, injection molding has become a cornerstone of modern manufacturing.
## The Injection Molding Process
The injection molding process consists of several key steps:
### 1. Clamping
The two halves of the mold are securely closed by the clamping unit before injection begins. Proper clamping ensures the mold remains closed during the injection process.
### 2. Injection
Plastic pellets are fed into the machine’s barrel, where they are heated until molten. The molten plastic is then injected into the mold cavity under high pressure.
### 3. Cooling
After injection, the plastic begins to cool and solidify within the mold. Cooling time varies depending on the material and part thickness.
### 4. Ejection
Once sufficiently cooled, the mold opens and the finished part is ejected. The mold then closes again, ready for the next cycle.
## Common Materials Used in Injection Molding
Various thermoplastic materials are suitable for injection molding, each with unique properties:
### Thermoplastics
Thermoplastics are the most commonly used materials in injection molding due to their ability to be melted and reformed multiple times. Common thermoplastics include:
- Polypropylene (PP)
- Polyethylene (PE)
- Polystyrene (PS)
- Acrylonitrile Butadiene Styrene (ABS)
- Polycarbonate (PC)
### Thermosetting Plastics
Though less common, thermosetting plastics can also be injection molded. These materials undergo a chemical change during molding and cannot be remelted:
- Epoxy resins
- Phenolic resins
- Polyurethane
## Applications of Injection Molding
Injection molding finds applications across numerous industries:
### Consumer Products
Many everyday items are produced through injection molding, including:
- Plastic containers
- Toys
- Household appliances
### Automotive Components
The automotive industry relies heavily on injection molding for:
Keyword: Injection Molding
- Dashboard components
- Bumpers
- Interior trim pieces
### Medical Devices
Injection molding is crucial for producing sterile, precise medical components:
- Syringes
- Surgical instruments
- Medical device housings
## Advantages of Injection Molding
Injection molding offers several significant benefits:
- High production rates
- Repeatable high tolerances
- Low labor costs
- Minimal scrap loss
- Ability to use multiple materials simultaneously
## Conclusion
Injection molding remains one of the most efficient and versatile manufacturing processes for plastic parts. Its ability to produce complex shapes with excellent dimensional accuracy at high volumes makes it indispensable across multiple industries. As material science advances and manufacturing technologies improve, injection molding continues to evolve, offering even greater possibilities for product designers and manufacturers.