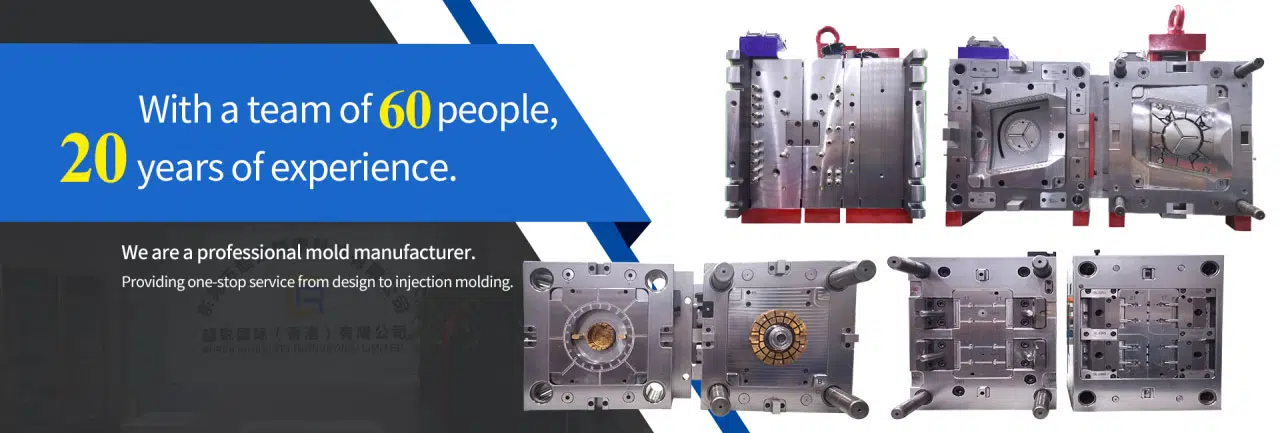
# Silk Screen Printing Techniques
## Introduction to Silk Screen Printing
Silk screen printing, also known as screen printing or serigraphy, is a versatile printing technique that has been used for centuries. This method involves creating a stencil (or screen) and using it to apply layers of ink onto a printing surface. While the name suggests the use of silk, modern screens are typically made from polyester or other synthetic materials.
## The Basic Process
The fundamental steps of silk screen printing include:
– Creating the design
– Preparing the screen
– Applying the emulsion
– Exposing the screen
– Washing out the unexposed emulsion
– Setting up for printing
– Applying the ink
– Curing the print
Keyword: Silk Screening
## Types of Silk Screen Printing
### 1. Flatbed Screen Printing
This is the most common method where the screen lies flat above the substrate. The squeegee moves across the screen, forcing ink through the mesh onto the material below.
### 2. Rotary Screen Printing
Used primarily in textile printing, this method employs cylindrical screens that rotate as the fabric moves beneath them. This allows for continuous patterns and high-speed production.
### 3. Manual Screen Printing
The traditional hand-operated method where each print is made individually. This is ideal for small batches and artistic applications where precision and control are paramount.
## Advanced Techniques
### Halftone Printing
This technique creates the illusion of continuous tone images through patterns of dots. By varying the size and spacing of these dots, printers can achieve photographic-quality results.
### Four-Color Process (CMYK)
Using cyan, magenta, yellow, and black inks, this method can reproduce full-color images by overlapping halftone patterns of each color.
### Discharge Printing
A specialized technique where the ink removes the dye from dark-colored fabrics rather than laying color on top, resulting in soft, breathable prints.
## Materials and Equipment
Successful silk screen printing requires several key components:
– Screens (frames with stretched mesh)
– Emulsions and sensitizers
– Squeegees of various sizes and hardness
– Printing inks (water-based, plastisol, discharge, etc.)
– Exposure units
– Drying/curing equipment
– Registration systems for multi-color prints
## Applications of Silk Screen Printing
This versatile technique finds applications in numerous industries:
– Textile and apparel (t-shirts, hoodies, etc.)
– Signage and posters
– Product labeling and packaging
– Printed electronics
– Ceramic and glass decoration
– Fine art reproduction
## Advantages of Silk Screen Printing
Some key benefits include:
– Ability to print on various surfaces
– Excellent opacity and color vibrancy
– Durability of prints
– Cost-effectiveness for medium to large runs
– Thick ink deposits for special effects
– Environmentally friendly options available
## Modern Innovations
Recent advancements in silk screen printing include:
– Digital screen making (direct emulsion output)
– UV-curable inks
– Automated printing systems
– Improved mesh materials
– Computerized registration systems
– Eco-friendly ink formulations
## Conclusion
Silk screen printing remains one of the most versatile and durable printing methods available today. From small art projects to large-scale industrial applications, its adaptability continues to make it relevant in our digital age. Whether you’re a hobbyist or a professional, mastering these techniques can open up a world of creative and commercial possibilities.